Laser processing machine tools apply the principle of laser cutting to cut plates into desired shapes. A станок лазерной резки mainly consists of two parts: the CNC operating table and the machine tool. The laser beam releases energy when it irradiates the workpiece’s surface, melting the material to achieve cutting.
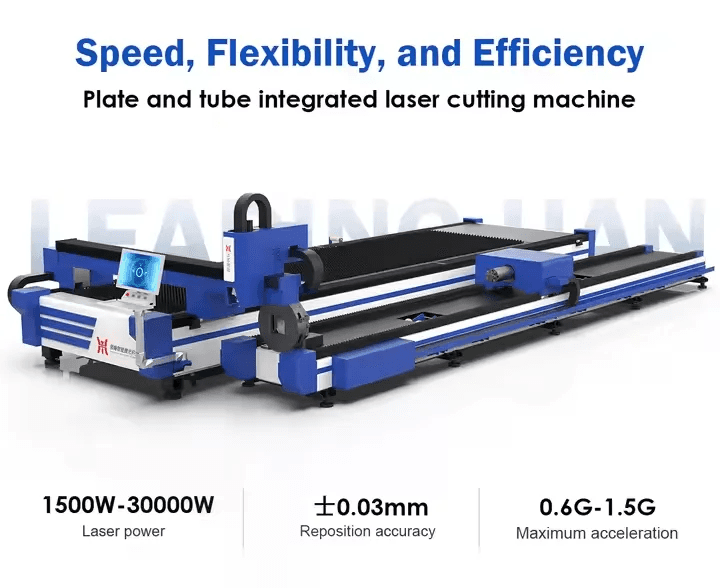
I. Advantages of Laser Cutting
The advantages of laser cutting machines enable their wide application in various fields.
1. High Efficiency
Laser cutting machines equip multiple CNC workbenches, allowing full CNC control of the cutting process. Operators can change the CNC program to cut parts of different shapes, including both two-dimensional and three-dimensional designs.
2. Fast Speed
A 1200W laser cuts 2mm mild steel at 600cm/min and 5mm polypropylene at 1200cm/min. Operators do not need to clamp the material during cutting.
3. Good Cutting Quality
A. The cutting edge of the машина лазерной резки пластин is narrow, the two sides of the slit are parallel and perpendicular to the surface, and the dimensional accuracy of the cut parts can reach ±0.05mm.
B. Laser cutting produces a smooth and beautiful cutting surface with a roughness of only tens of microns. It can serve as the final process, eliminating the need for mechanical processing, and allows users to directly use the parts.
C. Laser cutting produces a very small heat-affected zone, leaving the material’s performance near the slit almost unaffected. It also minimizes workpiece deformation, ensures high cutting accuracy, creates a good geometric shape for the slit, and forms a relatively regular rectangular cross-sectional shape.
4. Non-Contact Cutting
Laser cutting technology, as an efficient and precise processing method, demonstrates its core advantage through non-contact processing characteristics. A high-energy laser beam from the cutting gun processes the workpiece, eliminating the direct contact between the tool and the workpiece that occurs in traditional mechanical cutting. This approach significantly reduces tool wear and extends the equipment’s service life. Operators flexibly adjust the laser output power, frequency, focus position, and other parameters based on the material, thickness, and shape characteristics of different workpieces to achieve precise cutting.
Additionally, the laser cutting process exhibits low noise and low vibration characteristics, which not only improve the working environment but also reduce mechanical impact on the equipment structure. The use of a closed processing system effectively controls the dust and harmful gases generated during the cutting process, achieving low-pollution green processing. This approach aligns with the modern manufacturing industry’s requirements for environmental protection and sustainable development.
II. Cutting Principle
The principle of laser cutting focuses the high energy of the laser on the material to melt or vaporize it, thereby achieving cutting. This non-contact processing method offers high precision, high speed, and strong material adaptability, and industries widely use it in various manufacturing and material processing fields.
1. Laser Generator Generates Laser Beam
The laser generator in the plate laser cutting machine generates a high-energy, high-concentration laser beam. Commonly used laser types include CO2 laser, fiber laser and solid laser.
2. Laser Beam Guidance and Focusing
Optical devices guide and focus the laser beam into a small diameter spot. Lenses or mirrors usually control the path of the laser beam and focus it to a smaller point.
3. Material Absorbs Laser Energy
The material absorbs the energy of the laser when the laser beam hits its surface. Different materials vary in their absorption rates, and some metal materials absorb lasers at a higher rate.
4. Heating, Melting or Vaporizing of Materials
The high energy density of the laser heats the material quickly to the temperature of melting or vaporization. The material consumes a lot of heat energy during melting or vaporization to achieve cutting.
5. Auxiliary Gas Injection
Operators often inject auxiliary gas (such as nitrogen, oxygen, or inert gas) through the nozzle during the cutting process to protect the laser cutting area, blow away the melted material, and speed up the cutting process.
6. Motion Control System
A motion control system usually equips laser cutting machines for steel plates to control the movement path of the laser cutting machine head on the material’s surface. A computer program enables the cutting of various complex shapes.
Заключение
Laser cutting machine is widely used in various industries, such as metal processing, automobile manufacturing, electronic components, aerospace, etc. It can achieve high-precision and high-speed cutting, and is suitable for workpieces of different shapes and sizes. Laser cutting machine for steel plate is an advanced processing equipment. Understanding its working principle, laser characteristics, applicable materials, types, cutting parameters and application fields is essential to master its use and optimize the processing process.