Laser cutting machines have become indispensable in modern manufacturing, providing high precision, speed, and versatility for cutting a wide variety of materials. However, like any technology, achieving optimal cutting quality requires attention to several factors. In this blog, we’ll dive into some key strategies and considerations to enhance the cutting quality of your laser cutting machine. Let’s explore these aspects in greater detail:
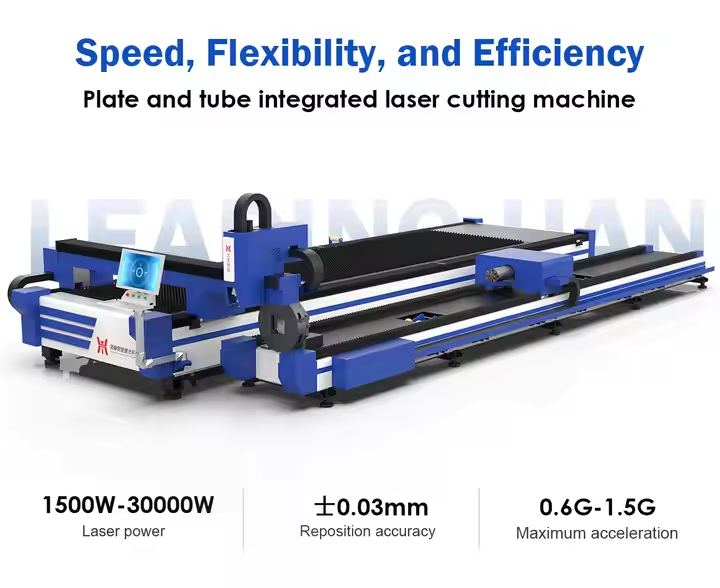
1. Choose the Right Laser Cutting Machine for Your Needs
Before diving into the specifics of improving cutting quality, it’s crucial to begin with the right equipment. Not all laser cutting machines are created equal. There are various types designed for specific tasks—like high frequency plate and tube integrated laser cutting machines—which are ideal for handling both flat plates and complex tube geometries.
When selecting a laser cutting machine, consider factors such as:
Material compatibility: The thickness and type of material you plan to cut will dictate the laser power you need.
Cutting speed: For faster production, you need a machine with an efficient cutting system that doesn’t compromise quality.
Precision: For intricate designs, ensure the laser cutting machine can offer the precision necessary to cut fine details accurately.
Choosing the right machine from a trusted laser cutting machine supplier can significantly impact the overall quality of your cuts.
2. Optimize Laser Power and Focus
One of the most critical elements in laser cutting is the proper adjustment of laser power. Too little power can result in incomplete cuts, while too much power can cause excessive heat, leading to poor cut quality, rough edges, or even material distortion. Similarly, focusing the laser beam at the optimal focal point is essential for clean and precise cuts.
Power settings: Adjust the laser power based on the thickness and type of material. For thinner materials, lower power settings are generally sufficient, while thicker materials require higher power.
Focus lens: Ensure the lens is clean and the focus is adjusted correctly. A misaligned focus point can lead to undercutting or overcutting.
Regularly recalibrate your laser cutting machine to maintain consistent power and focus for optimal results.
3. Optimize Cutting Speed
Cutting speed plays a vital role in the final quality of the cut. If the speed is too high, the laser will not be able to penetrate the material sufficiently, resulting in incomplete or rough cuts. On the other hand, if the speed is too slow, excessive heat will be applied, which could melt the material or create excessive slag on the cut edges.
Adjusting cutting speed should be done according to the material and thickness:
For metals like stainless steel: the cutting speed should be slower to allow the laser to fully cut through.
For materials like acrylic: you can increase the speed as they don’t require as much heat to cut.
Many laser cutting machine suppliers offer software that can help automate the speed adjustment process for specific materials and thicknesses, allowing for more consistent results.
4. Proper Material Preparation
Material quality can significantly affect the performance of your laser cutting machine. Ensure the material is free from contaminants like oil, rust, or dust, as these can interfere with the laser beam, leading to poor cutting quality.
Material flatness: The material must be flat before cutting. Warped or bent materials can cause uneven cuts, as the laser will not be able to focus evenly across the surface.
Thickness consistency: Materials with varying thickness can lead to inconsistent cutting speeds and uneven results.
Perform regular checks on the materials you’re using to ensure they are of high quality and properly prepared.
5. Use Software for Path Optimization
Modern laser cutting machines come equipped with software that optimizes the cutting path. Path optimization can reduce waste material, improve cutting speed, and enhance cut quality. By using software to pre-program cutting patterns, you can ensure that the laser travels the most efficient route.
Minimize unnecessary movement: Optimized software paths ensure the laser moves in the most efficient direction, reducing the overall cutting time and improving quality.
Reduce kerf: By adjusting the cutting path, the software can minimize kerf (the width of the cut), ensuring that parts fit together more accurately.
If you’re using a high frequency plate and tube integrated laser cutting machine, the software will often have advanced features tailored to the cutting of both flat and tubular materials, making it even more important to utilize these tools effectively.
6. Train Operators and Use Advanced Technologies
The skill of the operator can also have a significant impact on cutting quality. Training operators on how to properly adjust the laser cutting machine settings, troubleshoot common problems, and recognize issues early can help maintain high-quality results.
Moreover, some advanced technologies, such as fiber lasers and CO2 lasers, offer more precise and efficient cutting methods that may be suitable for your needs. Keeping up with new developments and adopting more advanced technologies can significantly improve cutting precision.
Заключение
Improving the cutting quality of your laser cutting machine requires a multifaceted approach, combining the right machine, optimized settings, proper material handling, and consistent maintenance. Whether you’re working with a high frequency plate and tube integrated laser cutting machine or a more traditional system, understanding these key factors will help you achieve better results in terms of precision, speed, and material efficiency. Always keep in mind that the quality of your machine and its operation can make or break your production process, so investing time in optimization is always a worthwhile endeavor.
By following these strategies and working with a reliable laser cutting machine supplier, you’ll be well on your way to achieving superior cutting quality and improving your overall manufacturing efficiency.