レーザー加工用工作機械は、レーザー切断の原理を応用して板材を目的の形状に切断する。A レーザー切断機 主にCNC操作テーブルと工作機械の2つの部分から構成される。レーザー光線は、被加工物の表面に照射されるとエネルギーを放出し、材料を溶かして切断を行う。
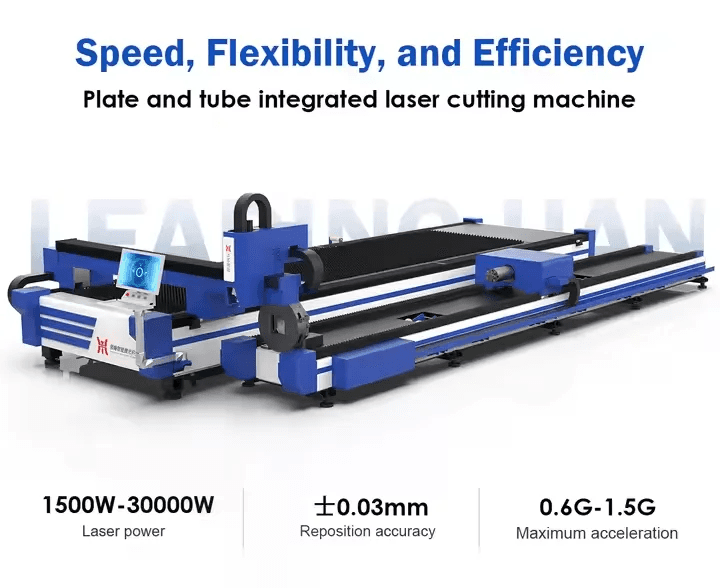
I.の利点 Lアサー Cユッティング
レーザー切断機の利点は、様々な分野での幅広い応用を可能にしている。
1. 高い E効率
レーザー切断機は複数のCNCワークベンチを装備しており、切断工程を完全にCNC制御することができる。オペレーターはCNCプログラムを変更することで、二次元や三次元のデザインを含むさまざまな形状の部品を切断することができる。
2.速い S小便をする
1200Wレーザーは、2mmの軟鋼を600cm/分、5mmのポリプロピレンを1200cm/分で切断する。オペレーターは切断中に材料をクランプする必要がない。
3.グッド Cユッティング Q品質
A.の最先端 プレートレーザー切断機 の幅は狭く、スリットの両側は表面に対して平行と垂直であり、切断部品の寸法精度は±0.05mmに達する。
B.レーザー切断は、数十ミクロンの粗さしかない滑らかで美しい切断面が得られる。機械的な加工を必要としない最終工程として機能し、ユーザーは部品を直接使用することができる。
C.レーザー切断では、熱影響部が非常に小さくなるため、スリット付近の材料性能はほとんど影響を受けません。また、ワークの変形を最小限に抑え、高い切断精度を確保し、スリットの幾何学的形状を良好にし、比較的規則的な長方形の断面形状を形成します。
4.非Cオンタクト Cユッティング
レーザー切断技術は、効率的で精密な加工方法として、非接触加工特性によってその核となる利点を発揮する。カッティングガンから照射される高エネルギーのレーザービームが加工物を加工するため、従来の機械的な切断で発生する工具と加工物の直接接触がなくなります。このアプローチにより、工具の摩耗が大幅に減少し、装置の耐用年数が延びます。オペレーターは、さまざまなワークの材料、厚さ、形状の特性に基づいて、レーザー出力、周波数、焦点位置、およびその他のパラメーターを柔軟に調整し、正確な切断を実現します。
さらに、レーザー切断工程は低騒音・低振動特性を示し、作業環境を改善するだけでなく、装置構造への機械的影響を低減する。また、クローズド加工システムの採用により、切断工程で発生する粉塵や有害ガスを効果的に抑制し、低公害のグリーン加工を実現している。このアプローチは、環境保護と持続可能な発展に対する現代の製造業の要求に合致している。
II.切断原理
レーザー切断の原理は、レーザーの高エネルギーを材料に集中させ、材料を溶融または気化させることで切断を実現する。この非接触加工法は、高精度、高速、強力な材料適応性を提供し、産業は広く様々な製造業や材料加工分野で使用されています。
1. レーザー Gエネレーター Gエネレーツ Lアサー Bイーム
プレートレーザー切断機のレーザー発振器は、高エネルギー、高集中のレーザービームを発振する。一般的に使用されるレーザーの種類には、CO2レーザー、ファイバーレーザー、ソリッドレーザーなどがある。
2. レーザー Bイーム G指導と Fオキュレーティング
光学デバイスは、レーザービームを誘導し、小径のスポットに集光します。レンズやミラーは通常、レーザービームの経路を制御し、より小さな点に集光します。
3. 素材 Aアンズ Lアサー Eエネルギー
レーザービームがその表面に当たると、材料はレーザーのエネルギーを吸収する。材料によってその吸収率は異なり、金属材料の中にはレーザーを高い吸収率で吸収するものもあります。
4. 暖房、 Mまたは Vの M資料
レーザーの高いエネルギー密度は、材料を溶融または気化の温度まで素早く加熱する。材料は、切断を達成するために、溶融または気化の間に多くの熱エネルギーを消費します。
5. 補助 Gとして I射出
オペレーターは、レーザー切断領域を保護し、溶融した材料を吹き飛ばし、切断プロセスを高速化するために、切断プロセス中にノズルから補助ガス(窒素、酸素、不活性ガスなど)を注入することが多い。
6. モーション Cコントロール Sシステム
モーションコントロールシステムは通常、鋼板用レーザー切断機に装備され、材料表面上でのレーザー切断機ヘッドの移動経路を制御する。コンピュータープログラムにより、様々な複雑形状の切断が可能。
結論
レーザー切断機は、金属加工、自動車製造、電子部品、航空宇宙など様々な産業で広く使用されている。高精度、高速切断が可能で、様々な形状、サイズのワークに適しています。 鋼板用レーザー切断機 は高度な加工機器である。その動作原理、レーザー特性、適用材料、種類、切断パラメータ、適用分野を理解することは、その使い方をマスターし、加工プロセスを最適化するために不可欠である。