In today’s fast-paced manufacturing world, flexibility is key to staying competitive. Companies must quickly adapt to changing demands, smaller batches, and increased customization. The 3015 plate tube laser cutting machine factory plays a vital role in this shift. These machines are central to the digital transformation of manufacturing processes. This article explores how plate and tube integrated laser cutting machines are revolutionizing production. They offer precision, versatility, and automation in industries where these factors are crucial.
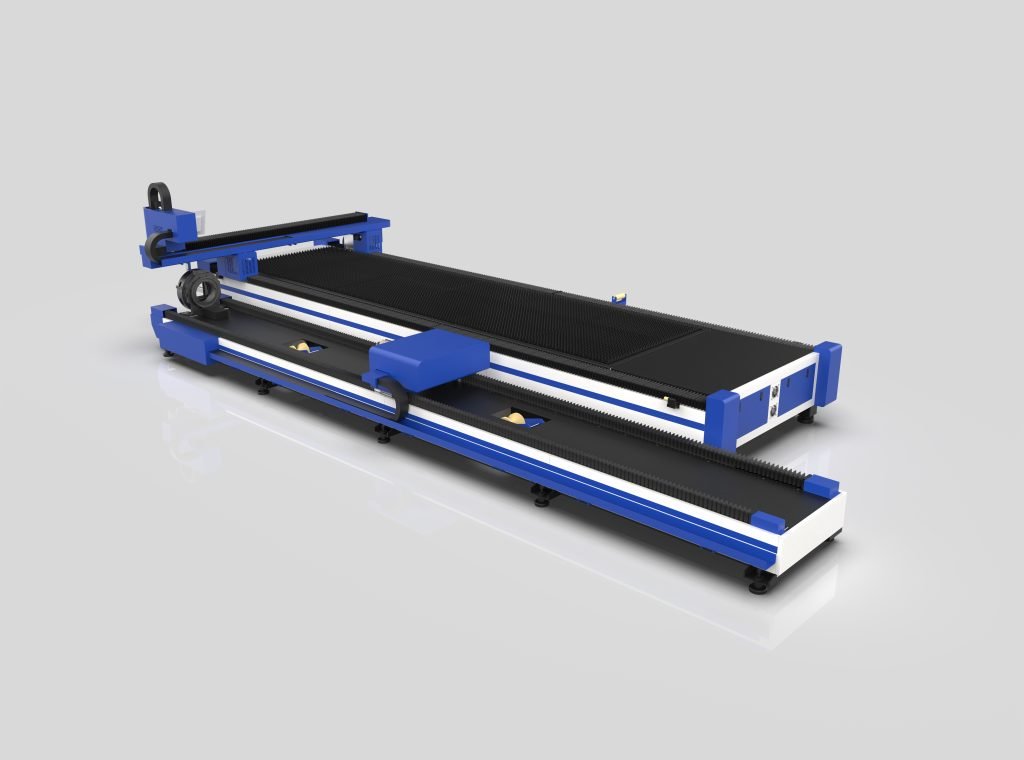
I. Meeting the Need for Flexibility
The rise of 3015 plate tube laser cutting machines aligns with the growing demand for flexibility. Traditional manufacturing models are no longer enough for modern needs. Companies now must produce a wide range of products in small, customized batches. The plate and tube integrated laser cutting machine addresses this challenge. It cuts pipes, tubes, and sheet metal within a single system. This innovation removes the need for multiple machines, streamlining operations and minimizing downtime.
Moreover, modern production lines need quick transitions without sacrificing speed or quality. The integrated nature of plate and tube laser cutting machines ensures seamless task changes. This ability is vital in industries like automotive, aerospace, and construction. These sectors rely on precision and the ability to customize components easily.
II. Enhancing Production Efficiency with Automation
Automation is a driving force behind flexible manufacturing’s digital transformation. The 3015 plate tube laser cutting machine factory leads this movement with advanced automation features. These machines come with sensors and real-time data collection systems. They also use machine learning algorithms to complete complex tasks with little human input.
For instance, tasks like material loading and cutting path optimization are automated. This dramatically boosts productivity while reducing human errors. Automation also ensures consistency in the quality of the output. With these technologies, manufacturers can focus on high-value work, like design and innovation. Meanwhile, the machines handle the repetitive tasks in the production process.
III. Real-Time Data Integration for Smarter Manufacturing
Real-time data collection allows manufacturers to monitor and adjust processes instantly. Plate and tube integrated laser cutting machines excel in this area with advanced data connectivity. They communicate with the factory’s digital infrastructure, optimizing production workflows.
These machines collect real-time data on cutting speed, material usage, and efficiency. Manufacturers can use this data to improve operations, reduce waste, and minimize downtime. The machines also adjust cutting parameters automatically based on real-time conditions. This adaptability helps align production with Industry 4.0 standards, boosting efficiency.
IV. Software Integration for Streamlined Operations
The seamless integration of hardware and software is essential for flexible manufacturing. The plate and tube integrated laser cutting machine often comes equipped with cutting-edge software. This software works smoothly with existing factory systems to optimize production.
For example, manufacturers can program cutting patterns and monitor machine health. They can even simulate production runs before actual execution. CAD/CAM software allows designs to be sent directly to the plate tube laser cutting machine. This reduces setup time and increases cutting accuracy. Additionally, remote monitoring provides greater oversight, allowing manufacturers to control operations from anywhere.
V. Reducing Waste for Sustainability
Sustainability has become a growing priority for many manufacturing operations. The plate and tube integrated laser cutting machine plays a crucial role in minimizing waste. Its precise cutting ensures more efficient use of raw materials during production.
Traditional methods often result in material offcuts and waste. However, the accuracy of laser cutting reduces this significantly. The software also optimizes cutting patterns to further reduce waste. This focus on sustainability not only benefits the environment but also cuts costs for manufacturers. By using fewer resources, companies can achieve more without excess.
VI. Shortening Lead Times for Competitiveness
Speed is essential for maintaining a competitive edge, especially in fast-moving industries. The 3015 plate tube laser cutting machine factory reduces lead times by integrating multiple cutting processes. This means less time spent on machine changes and production setups.
Manufacturers can produce high-quality, customized parts more quickly, giving them an advantage. This capability is particularly useful in industries like automotive and aerospace. These sectors face rapidly changing customer demands, and quick turnaround times are crucial for success.

VII. Conclusion
In summary, plate and tube integrated laser cutting machines are central to the digital transformation of flexible manufacturing. These machines enhance production efficiency, enable real-time data integration, and reduce waste. As automation and software integration evolve, these machines will become even more vital in manufacturing processes.
The need for customized, efficient, and sustainable production solutions continues to grow. Technologies like the 3015 plate tube laser cutting machine factory are meeting these needs. By revolutionizing the way manufacturers approach production, these machines are shaping the future of smart, flexible manufacturing.