Laser welding machines are revolutionizing the welding industry with their precision, efficiency, and versatility. As a cutting-edge technology, they bring numerous advantages to various sectors, from automotive manufacturing to aerospace engineering. In this article, we will explore how laser welding machines are transforming the welding process and reshaping industrial practices.
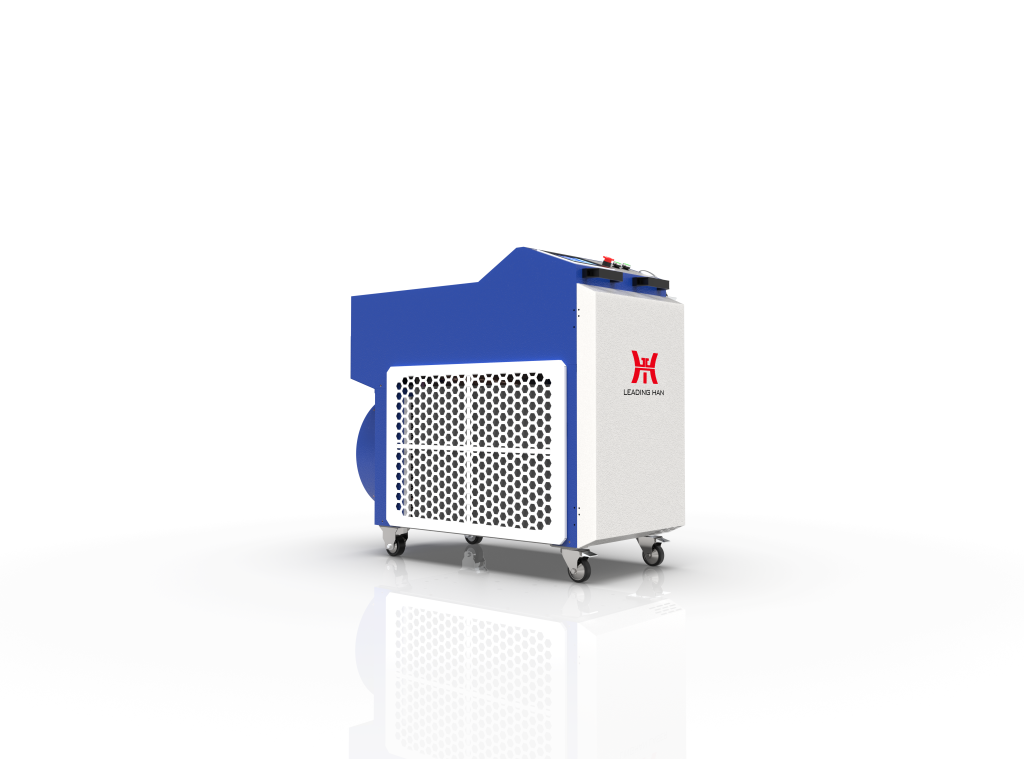
I. Unmatched Precision in Welding
Laser welding machines offer exceptional precision compared to traditional welding methods. The focused laser beam provides a high level of control over the welding process. This precision is essential for industries that require detailed and delicate work. For instance, in the electronics sector, where small components are welded together, a laser’s pinpoint accuracy is invaluable. The ability to weld microscopic parts with minimal distortion makes laser welding indispensable.
II. High Welding Speed
One of the key advantages of laser welding machines is their speed. These machines can complete welding tasks much faster than conventional welding techniques. This speed is especially important in high-production industries, such as automotive and aerospace, where efficiency directly impacts profitability. With laser welding, companies can increase production rates without sacrificing quality, making it a game-changer for large-scale operations.
III. Reduced Heat Affected Zone
Traditional welding methods often generate significant heat, which can damage surrounding materials. Laser welding machines, however, produce a highly concentrated heat source, reducing the heat-affected zone (HAZ). This minimized HAZ ensures that the integrity of the surrounding material remains intact. For industries working with sensitive or heat-reactive materials, such as medical devices or specialized alloys, this feature is crucial for maintaining product quality.
IV. Versatility Across Materials
Laser welding machines are highly versatile and can be used on a wide range of materials. From metals like aluminum and stainless steel to more exotic materials like titanium, these machines can handle diverse welding tasks. This versatility makes laser welding an ideal choice for industries that work with multiple material types, eliminating the need for different welding equipment.
V. Cleaner and Environmentally Friendly
Compared to traditional welding techniques, laser welding machines produce minimal waste and spatter. This cleaner process results in less material waste and reduces the need for post-welding cleanup. Moreover, laser welding is more energy-efficient, making it an environmentally friendly alternative. As industries move towards greener manufacturing processes, the adoption of laser welding aligns with sustainability goals.
VI. Integration with Automation Systems
The compatibility of laser welding machines with automation systems further enhances their utility. In modern manufacturing, automation plays a significant role in improving consistency and reducing human error. Laser welding machines can easily be integrated into robotic systems for fully automated welding processes. This level of automation boosts productivity and ensures consistent, high-quality welds across large production runs.
VII. Improved Welding of Complex Geometries
Complex geometries often pose a challenge for traditional welding techniques. However, laser welding machines excel in welding intricate shapes and structures. The precise control of the laser beam allows for welding in hard-to-reach areas or on complex components. This makes laser welding particularly useful in industries like aerospace, where parts often have irregular shapes and require precise welding.
VIII. Enhanced Weld Strength and Durability
Weld strength is a critical factor in many industries, and laser welding machines provide strong, durable welds. The high energy density of the laser beam ensures deep penetration, resulting in a strong bond between the materials. This leads to welds that can withstand high stress and pressure, which is essential in industries like automotive and aerospace, where component reliability is paramount.
IX. Minimal Distortion of Workpieces
The concentrated energy from laser welding machines results in less thermal expansion and contraction during the welding process. This means there is less distortion of the workpiece compared to traditional welding methods. For industries where precision and dimensional accuracy are crucial, such as the production of medical devices or precision instruments, laser welding offers a distinct advantage.
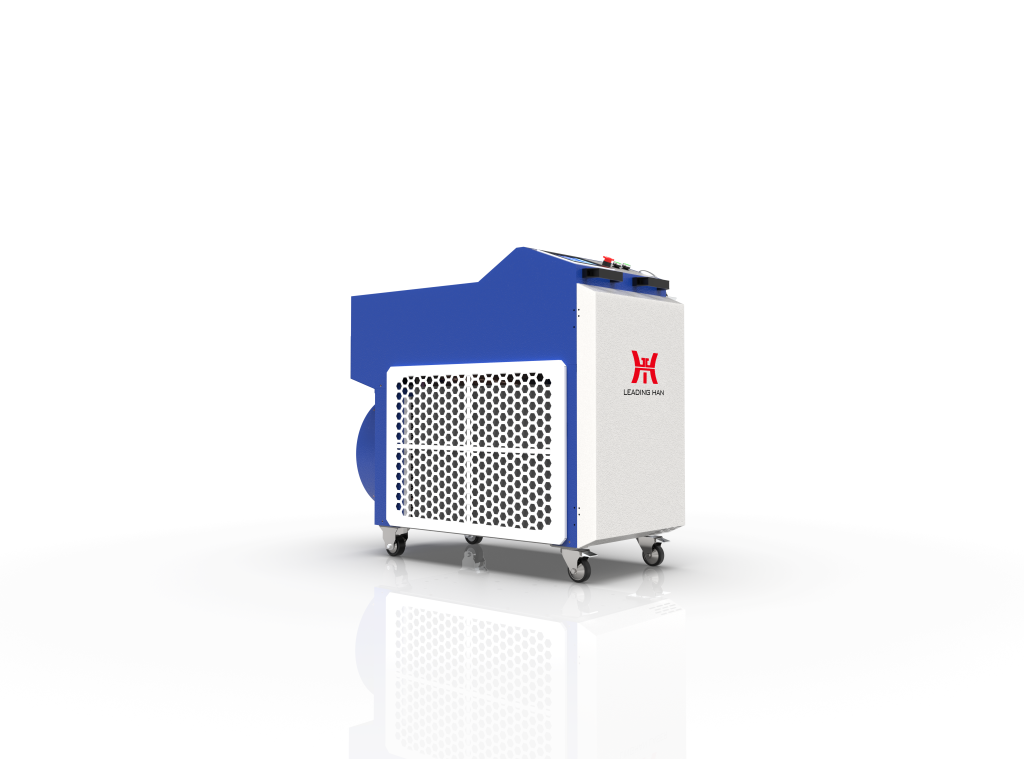
X. Future Trends in Laser Welding Technology
As technology continues to evolve, laser welding machines will likely see further advancements. The integration of artificial intelligence and machine learning may lead to smarter laser welding systems that can self-correct in real-time, ensuring even higher levels of precision and efficiency. Additionally, as industries push towards more sustainable manufacturing processes, laser welding will play a pivotal role due to its energy efficiency and reduced waste.
XI. Conclusion
Laser welding machines are revolutionizing the welding industry by offering unmatched precision, speed, and versatility. Their ability to handle a wide range of materials, create strong and durable welds, and minimize waste makes them a valuable asset in modern manufacturing. As industries continue to adopt more automated and environmentally friendly technologies, laser welding is set to become a cornerstone of industrial innovation.