Laser welding machines have revolutionized the manufacturing industry with their precision, efficiency, and versatility. These machines utilize a highly focused laser beam to join materials, making them ideal for a wide range of applications, from automotive to aerospace industries. In this blog, we will discuss the common welding processes of laser welding machines, their advantages, and how to choose the best laser welding machine for your needs.
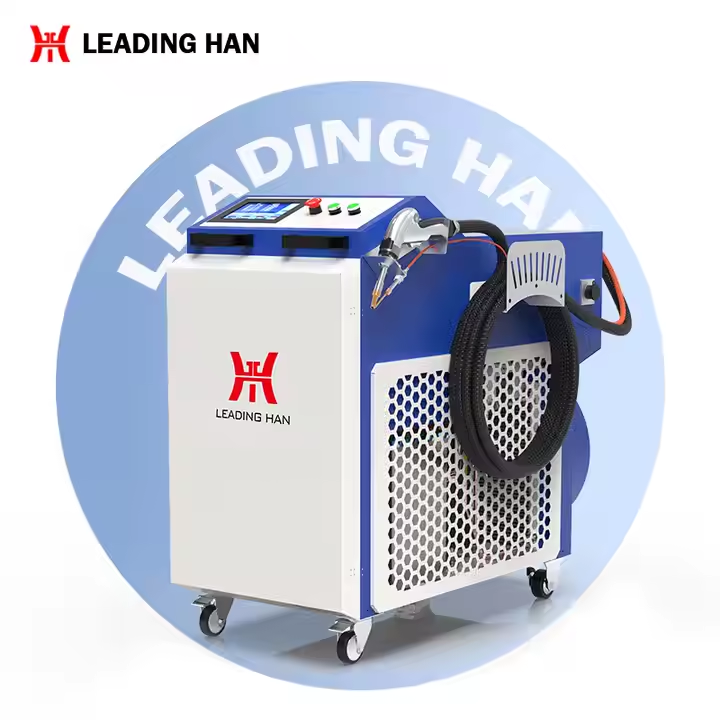
1. Introduction to Laser Welding Machines
Laser welding machines are advanced tools that use a concentrated beam of light to melt and fuse materials together. The laser beam is generated by a laser source and directed through a series of mirrors or fiber optics to the workpiece. The intense heat generated by the laser beam allows for precise control over the welding process, resulting in strong, clean, and high-quality welds.
One of the key advantages of laser welding machines is their ability to weld a wide variety of materials, including metals, plastics, and even ceramics. This versatility makes them indispensable in industries where precision and durability are paramount. Additionally, laser welding machines offer several benefits over traditional welding methods, such as reduced heat-affected zones, minimal distortion, and the ability to weld complex geometries.
2. Common Welding Processes of Laser Welding Machines
2.1. Conduction Welding
Conduction welding is a process where the laser beam heats the surface of the material to its melting point, causing the material to flow and fuse together. This process typically applies to thin materials or applications requiring a shallow weld depth. Conduction welding produces smooth and aesthetically pleasing weld seams, making it ideal for applications in the jewelry and electronics industries.
2.2. Keyhole Welding
Keyhole welding, also known as deep penetration welding, involves using a high-power laser beam to create a “keyhole” or vapor cavity in the material. The keyhole allows the laser beam to penetrate deeply into the material, resulting in a strong and deep weld. This process is commonly used for thicker materials or applications where high weld strength is required, such as in the automotive and aerospace industries.
2.3. Hybrid Welding
Hybrid welding combines laser welding with another welding process, such as arc welding or gas metal arc welding (GMAW). This combination allows for the benefits of both processes, such as the high precision of laser welding and the high deposition rate of arc welding. Hybrid welding is often used in applications where high welding speeds and deep penetration are required, such as in the shipbuilding and heavy machinery industries.
2.4. Spot Welding
Spot welding focuses the laser beam on a small area to create a weld spot. Manufacturers commonly use this process to join thin sheets of metal or to create a series of small, discrete welds. The automotive industry widely employs spot welding for joining body panels and other components.
2.5. Seam Welding
Seam welding involves using a continuous laser beam to create a long, continuous weld along a seam. Manufacturers commonly use this process to join sheets of metal or to create leak-proof seals, such as in the production of fuel tanks or pressure vessels. The automotive and aerospace industries often utilize seam welding for these applications.
3. Advantages of Laser Welding Machines
3.1. Precision and Control
One of the most significant advantages of laser welding machines is their ability to provide precise control over the welding process. The focused laser beam allows for accurate placement of the weld, resulting in minimal heat-affected zones and reduced distortion. This precision is particularly important in industries where tight tolerances and high-quality welds are required.
3.2. Speed and Efficiency
Laser welding machines are capable of welding at high speeds, making them ideal for high-volume production environments. The ability to quickly and efficiently join materials can significantly reduce production times and increase overall productivity. Additionally, the reduced heat input and minimal post-welding cleanup further contribute to the efficiency of laser welding machines.
3.3. Versatility
Laser welding machines are highly versatile and can be used to weld a wide range of materials, including metals, plastics, and ceramics. This versatility makes them suitable for a variety of applications across different industries. Whether you are working with thin sheets of metal or thick plates, a laser welding machine can provide the precision and strength needed for your application.
3.4. Reduced Heat-Affected Zones
Traditional welding methods often result in large heat-affected zones, which can weaken the material and lead to distortion. Laser welding machines, on the other hand, produce minimal heat-affected zones, resulting in stronger and more durable welds. This is particularly important in applications where the integrity of the material is critical, such as in the aerospace and medical industries.
4. Choosing the Best Laser Welding Machine
When it comes to selecting the best laser welding machine for your needs, there are several factors to consider. These include the type of materials you will be welding, the thickness of the materials, the required weld strength, and the production volume. Additionally, it is important to consider the power and precision of the laser welding machine, as well as its ease of use and maintenance.
One of the most important factors to consider is the reputation and reliability of the laser welding machine manufacturer. A reputable manufacturer will provide high-quality machines that are built to last and offer excellent performance. They will also provide comprehensive support and service, ensuring that your laser welding machine operates at peak efficiency for years to come.
Conclusion
Laser welding machines have become an essential tool in modern manufacturing, offering precision, efficiency, and versatility. Whether you are working in the automotive, aerospace, or electronics industry, a laser welding machine can provide the high-quality welds you need to meet your production goals. By understanding the common welding processes of laser welding machines and choosing the best laser welding machine from a reliable laser welding machine manufacturer, you can ensure that your welding operations are efficient, reliable, and produce the highest quality results.
In conclusion, laser welding machines are a powerful and versatile tool that can significantly enhance your manufacturing processes. By investing in the right machine and working with a trusted manufacturer, you can achieve the precision, efficiency, and quality that your business demands.