In today’s manufacturing environment, precision, speed, and efficiency are essential for staying competitive. One technology that has dramatically impacted the industry is the laser sweismasjien. This innovative tool allows for high-precision welding with minimal heat distortion and an increased speed of operation. Whether you’re in the automotive, aerospace, electronics, or medical device industries, a laser welding machine can significantly improve your production efficiency. However, simply owning a laser welding machine isn’t enough—it’s how you use it that truly matters. In this blog post, we’ll discuss strategies to maximize the use of laser welding machines to boost production efficiency, reduce costs, and maintain high-quality standards.
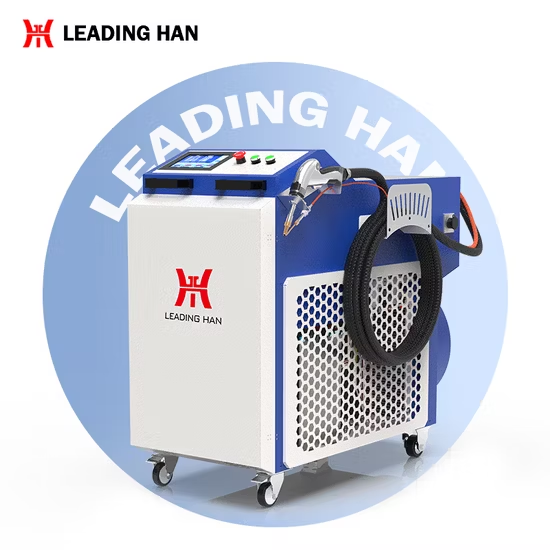
1. Optimizing Settings for Different Materials
Laser welding machines offer the flexibility to weld a wide range of materials, from metals to thermoplastics. However, different materials require different settings, such as laser power, speed, focal length, and beam size. By optimizing these parameters for specific materials, you can significantly increase both the quality of the welds and production speed. For instance, welding stainless steel may require a different laser power setting than welding aluminum. Understanding the characteristics of the material you’re working with and adjusting the laser settings accordingly ensures a strong, clean weld and reduces the chances of defects.
By having a well-calibrated laser welding machine, operators can reduce downtime, improve the consistency of welds, and lower the need for rework, all of which contribute to better overall efficiency. Furthermore, automation systems can be used in conjunction with the welding machine to streamline operations, especially for high-volume production runs.
2. Training Operators and Technicians
One of the most common reasons for inefficiency in laser welding operations is a lack of proper training. A laser welding machine is a sophisticated piece of equipment, and without adequate training, operators may make mistakes or fail to operate the machine to its full potential. Proper training ensures that operators can adjust settings correctly, handle different materials, and troubleshoot common issues efficiently.
Training also ensures that workers understand the importance of maintenance and safety, which can prevent costly breakdowns or accidents. As part of a continuous improvement process, companies should encourage operators to engage in ongoing education, such as workshops or online training programs.Investing in operator education is an essential step toward optimizing the performance of a laser welding machine and improving overall production efficiency.
3. Regular Maintenance and Calibration
Laser welding machines are precision instruments, and to maintain peak performance, they need regular maintenance and calibration. Ensuring the laser beam is aligned properly and the optics are clean is crucial to the quality of the welds and to the longevity of the machine. A well-maintained laser welding machine operates more efficiently, with fewer breakdowns and less downtime.
Preventive maintenance schedules should be created and followed rigorously. This includes cleaning the lens and other components, checking the power settings, and ensuring the cooling systems are functioning properly. Regular calibration also guarantees that the machine operates at the correct settings, reducing the chances of inconsistent welds or material defects that could slow down production.
4. Utilizing Automation for Increased Throughput
Laser welding technology can be integrated with automation systems to further enhance production efficiency. Automated feeding systems, robotic arms, and conveyor belts can load and unload workpieces with minimal human intervention. This not only speeds up the process but also reduces the likelihood of errors caused by manual handling. By integrating robotics with a laser welding machine, manufacturers can achieve high-volume, continuous production with minimal human oversight.
Automation also allows for 24/7 production, as machines can be operated during off-hours, further boosting efficiency and output. The use of automated systems can also reduce labor costs and improve overall precision, as robots can handle repetitive tasks more consistently than human workers.
5. Laser Welding Machine Price vs. Investment Value
When considering a laser welding machine for sale, it’s essential to take into account not just the laser sweismasjien prys, but also the long-term value it can bring to your production line. While the initial investment may seem high compared to traditional welding equipment, the operational savings, reduced scrap, and higher production rates can offset the upfront costs over time.
Additionally, laser welding machines require less post-processing, such as grinding or polishing, compared to other methods like MIG or TIG welding. This reduces the need for additional labor and materials, contributing to cost savings in the long run. Therefore, when evaluating laser welding machine price, always consider the return on investment (ROI) based on production efficiency, quality improvements, and long-term cost reductions.
6. Improving Process Control with Real-Time Data
Another way to maximize the effectiveness of a laser welding machine is by incorporating advanced monitoring and control systems. These systems provide real-time data on welding parameters, such as power, speed, and heat input. By analyzing this data, manufacturers can make adjustments on the fly, optimizing the welding process and preventing defects.
For example, if the system detects that the laser power is fluctuating outside of the optimal range, it can automatically adjust the settings to maintain a consistent weld. This data-driven approach not only improves weld quality but also allows for predictive maintenance, helping to identify potential issues before they lead to machine failure.
7. Reducing Waste and Improving Yield
Laser welding is known for its minimal heat-affected zone (HAZ) and reduced distortion, which leads to a higher-quality weld with less waste. Unlike traditional welding methods that may require post-weld cleaning or additional material to compensate for imperfections, laser welding machines offer precision that minimizes the need for extra materials and reduces scrap.
By ensuring that the machine operates at optimal settings, manufacturers can further reduce waste and improve yield. This not only enhances production efficiency but also contributes to sustainability by lowering material consumption and reducing environmental impact.
Gevolgtrekking
Maximizing the use of a laser welding machine is not just about purchasing the right equipment but also about leveraging its full potential. By optimizing settings, training operators, maintaining equipment, utilizing automation, and considering the long-term investment value, manufacturers can significantly improve production efficiency. When considering a laser welding machine for sale, take the time to evaluate both the laser welding machine price and the expected ROI to make a well-informed decision.
Laser welding technology is an invaluable tool for industries that demand precision and high-quality welds. By investing in the right equipment, training, and processes, manufacturers can stay ahead of the competition and continually improve their production efficiency.