As modern manufacturing industries increasingly demand precision processing and efficient production, laser welding technology has rapidly gained popularity across various sectors. From automobiles and aerospace to medical devices and electronics, laser sweismasjiene are transforming traditional welding methods. Laser welding offers unique advantages like high precision, high efficiency, and minimal heat-affected zones, making it a preferred choice for many industries.
In this article, we will dive into the core components of a laser welding machine and explain its working principles, helping you better understand this advanced piece of equipment.
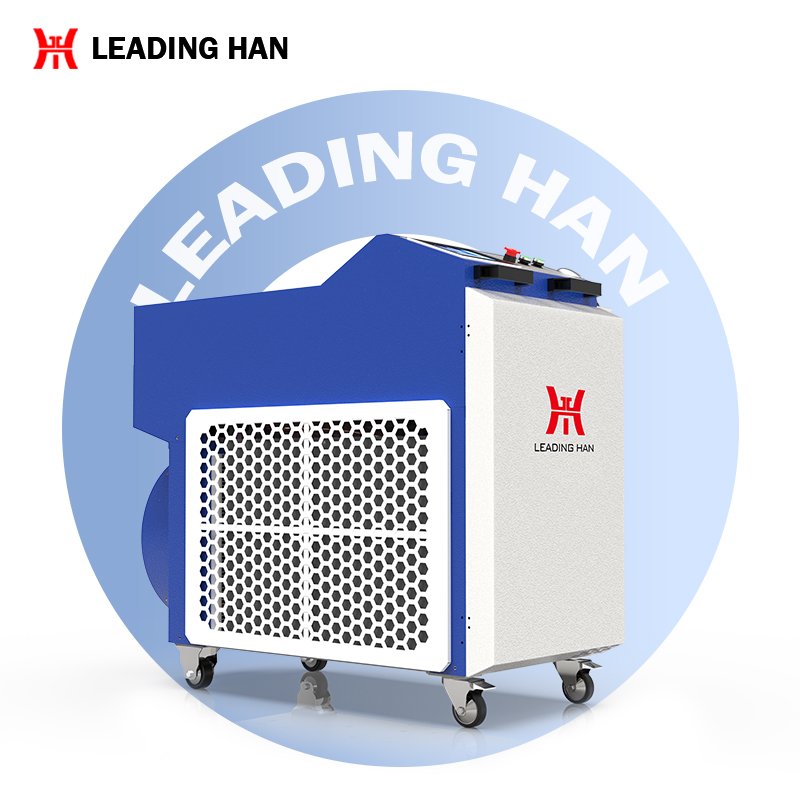
1. Overview of the Laser Welding Machine
Laser welding machines use a laser beam as a heat source to melt and fuse two metal parts together. Compared with traditional arc welding, laser welding has several advantages: faster welding speed, smaller heat-affected zone, and higher weld quality. In addition, laser welding can be automated and is suitable for welding parts with complex shapes and small volumes. This greatly improves production efficiency and welding accuracy.
The working principle of the laser welding process is to use a laser generator to generate a laser beam, which is focused on the surface of the workpiece through an optical system. The laser heats the metal to the melting point to form a local molten pool. As the laser continues to irradiate the molten pool, the molten pool expands, and the metal cools and solidifies to complete the welding process.
2. Core Components of a Laser Welding Machine
2.1 Laser Generator
The laser generator is the “heart” of the laser welding machine. Its main function is to generate a laser beam. The laser generator excites the laser medium to emit laser through mechanisms such as current and voltage, and the laser beam is transmitted to the surface of the workpiece through an optical system.
At present, there are three main types of laser generators: solid lasers, gas lasers, and fiber lasers. Each type has a different working principle, but can produce high-intensity, high-brightness lasers.
Fiber lasers: Fiber lasers are the most widely used type of laser generators. Fiber lasers have high electro-optical conversion efficiency, long service life, and strong adaptability. Fiber lasers can transmit laser beams through optical fibers, with a smaller focus, making them ideal for precision welding.
CO2 lasers: CO2 lasers use CO2 gas as a laser medium and emit lasers with a longer wavelength, which is suitable for welding certain materials, but have lower precision than fiber lasers.
YAG Lasers: YAG lasers use yttrium aluminum garnet (YAG) as the laser medium. They are known for their high laser power and stability, making them ideal for welding metals.
2.2 Optical System
The optical system is a crucial component responsible for transmitting and focusing the laser beam in a laser welding machine. It consists of components such as laser lenses, mirrors, and focusing lenses. The laser beam generated by the laser generator is directed by a series of mirrors to a focusing lens, which focuses it onto the workpiece.
Laser Lenses: These are used to focus the laser onto a very small spot. The lens’s focal length is adjusted to control the diameter of the laser beam, affecting the weld quality.
Mirrors: Mirrors redirect the laser beam along different paths, ensuring it reaches the required area for welding.
2.3 Focusing and Focus System
The size of the laser beam’s focal point significantly impacts the welding quality. The focusing system controls the laser beam’s focal point, which influences the welding depth and width. Generally, a smaller focal diameter is suitable for precise welding, while a larger focal diameter is better for wide-area welding.
Focus control is typically achieved by adjusting the position of the focusing lens. Accurate focus control is crucial to ensure the welding depth and quality are consistent.
2.4 Laser Scanning Galvo
The laser scanning galvo system is responsible for controlling the path of the laser beam in a laser welding machine. Using two high-speed rotating mirrors, the laser beam can rapidly move across the workpiece, allowing for precise welding on different areas. The speed and precision of the galvo system directly affect the welding efficiency and quality.
This scanning system is often used when welding paths need to change rapidly or when complex welding trajectories are required. The fast response time of the galvo system makes it ideal for high-speed welding applications.
2.5 Welding Head
The welding head is the component that comes into contact with the workpiece in a laser welding machine. It typically includes the focusing lens, protective lens, and gas protection system. The welding head’s primary function is to focus the laser onto the workpiece surface and to protect the welding area by using shielding gas to prevent oxidation and contamination.
Protective Gas: Shielding gas (such as nitrogen or argon) is used to protect the welding area during the laser welding process. It prevents exposure to air, reducing the risk of defects such as porosity and oxidation. The flow and purity of the shielding gas are essential to achieving high-quality welds.
Gas Nozzles: Through gas nozzles, the shielding gas is evenly distributed over the welding area, further ensuring the quality of the weld.
2.6 Control System
The control system is the “brain” of a laser welding machine, responsible for managing the welding process. It includes functions such as CNC (Computer Numerical Control) systems, laser output power control, and welding parameter adjustments. The precision and flexibility of the control system determine the stability of the welding process and the final weld quality.
Modern laser welding machines feature advanced CNC systems for precise control over laser power, speed, and path. By adjusting these parameters, different materials and thicknesses can be welded with high precision.
2.7 Water Cooling System
Due to the high energy output of the laser, large amounts of heat are generated during the welding process. To maintain normal operation and prevent overheating, an efficient cooling system is essential. The water cooling system circulates coolant to absorb the heat generated by the equipment, ensuring that key components like the laser generator remain within their operating temperature range.
3. Working Principle of a Laser Welding Machine
The laser welding process can be broken down into several key steps:
3.1 Laser Generator Produces the Laser Beam: The laser generator excites the laser medium, emitting a high-intensity laser beam.
3.2 Laser Beam is Transmitted by the Optical System: The laser beam passes through mirrors and focusing lenses, ultimately being focused onto a small point.
3.3 Laser Heats the Metal and Forms a Molten Pool: When the laser beam strikes the metal surface, the metal is rapidly heated to its melting point, creating a molten pool.
3.4 The Molten Pool Cools and Forms the Weld: As the laser beam moves, the molten pool gradually solidifies, forming a durable weld joint.
3.5 Shielding Gas is Applied: During the welding process, shielding gas is directed to the weld zone, preventing oxidation and contamination, ensuring high-quality results.
Gevolgtrekking
The laser welding machine is a key tool in modern manufacturing, offering superior performance and versatility across various industries. By understanding the core components and working principles of the equipment, you can better appreciate its benefits and how it can optimize your production. If you’re considering investing in a laser welding machine, whether a 1000W model for sale or from a reputable manufacturer, this advanced technology is a valuable investment.
We hope this article has helped you understand the workings of a laser welding machine. If you have any questions or would like more information about our products, please feel free to contact us.