Manufacturing industries face various risks in hazardous environments. Welding is one such process where safety concerns arise. Laser welding machines are now playing a pivotal role in enhancing safety standards. This article explores how laser welding machines and auto laser welding machines are reducing risks and improving workplace safety.
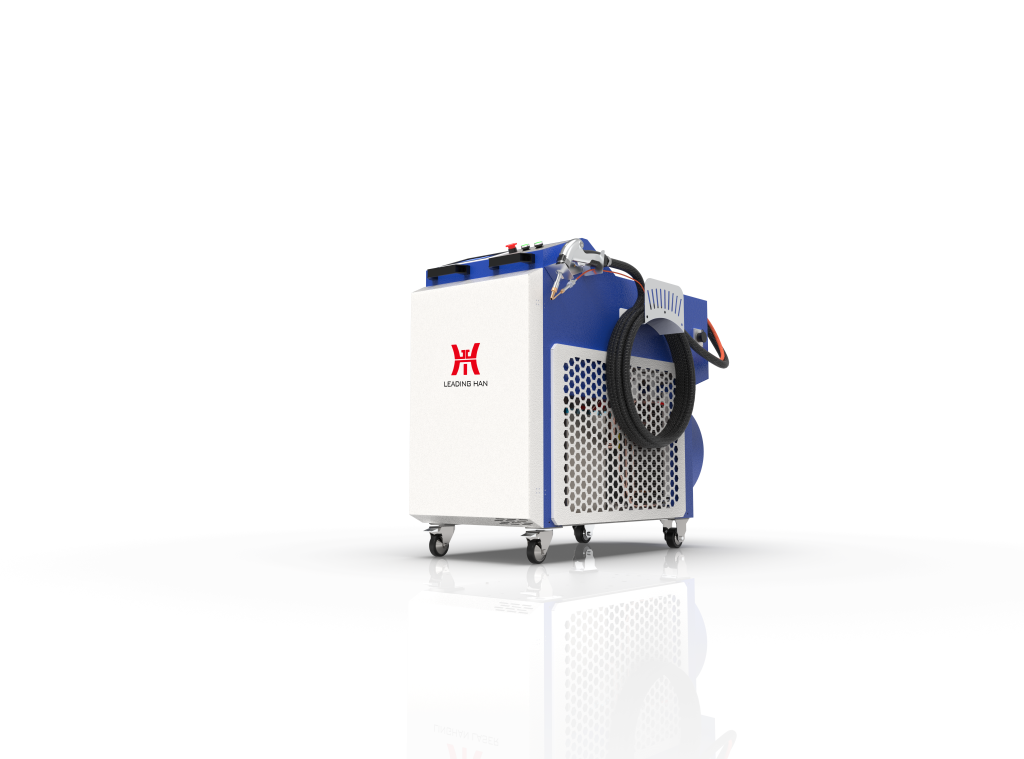
I. The Safety Challenges in Welding
Traditional welding methods pose numerous safety hazards. Workers are exposed to heat, toxic fumes, and sparks. Manual welding in hazardous environments increases the risk of accidents. Reducing human exposure to these dangers is essential for safe operations. Laser welding machines offer a safer alternative by reducing the need for manual involvement.
II. Precision and Control
Laser welding machines provide unmatched precision. This accuracy reduces the risk of error, ensuring safer operations. Unlike traditional welding, auto laser welding machines can be programmed for specific tasks. This control minimizes the chance of accidents caused by human error. The ability to precisely control the laser beam also reduces the likelihood of fire hazards.
III. Non-Contact Process
A key advantage of laser welding machines is their non-contact nature. Workers do not need to handle materials directly. This eliminates risks like burns and exposure to dangerous fumes. Auto laser welding machines further enhance safety by automating the entire process. This automation reduces the need for operators to be near high-risk areas.
IV. Reduced Heat Exposure
Laser welding machines produce focused, concentrated heat. This limits the heat-affected zone (HAZ). As a result, surrounding materials remain cooler, reducing the risk of fires or burns. The smaller HAZ ensures a safer working environment. In contrast, traditional welding methods expose larger areas to heat, increasing the chance of accidents.
V. Minimizing Toxic Fumes
Welding can produce harmful fumes, posing a risk to workers. In hazardous environments, this issue becomes more critical. Laser welding machines significantly reduce fume generation. Their precision and focused energy help minimize the release of dangerous gases. Auto laser welding machines further improve safety by keeping workers away from the fume source.
VI. Integration with Safety Systems
Auto laser welding machines can integrate with advanced safety systems. These systems monitor the welding process in real time. If any anomaly occurs, the machine can shut down automatically. This proactive safety feature prevents accidents before they happen. Integrating safety protocols with the machine ensures a more secure working environment.
VII. Automation and Remote Operation
One of the most significant safety benefits is automation. Auto laser welding machines allow for remote operation. Workers can control the machine from a distance, away from hazardous zones. This reduces direct human involvement in dangerous areas. In hazardous environments, such as nuclear facilities or chemical plants, this feature is particularly valuable.
VIII. Consistent and Reliable Welding
Human error is a major cause of accidents in manual welding. Auto laser welding machines provide consistent, reliable results. Automation ensures uniform welds every time, reducing the risk of mistakes. Consistency improves safety by eliminating the unpredictability of manual welding processes.
IX. Enhanced Monitoring and Real-Time Adjustments
Advanced laser welding machines come with monitoring systems. These systems track the welding process in real-time. If something goes wrong, adjustments can be made instantly. This reduces the chance of accidents during welding. The machine can self-correct, ensuring safety without human intervention.
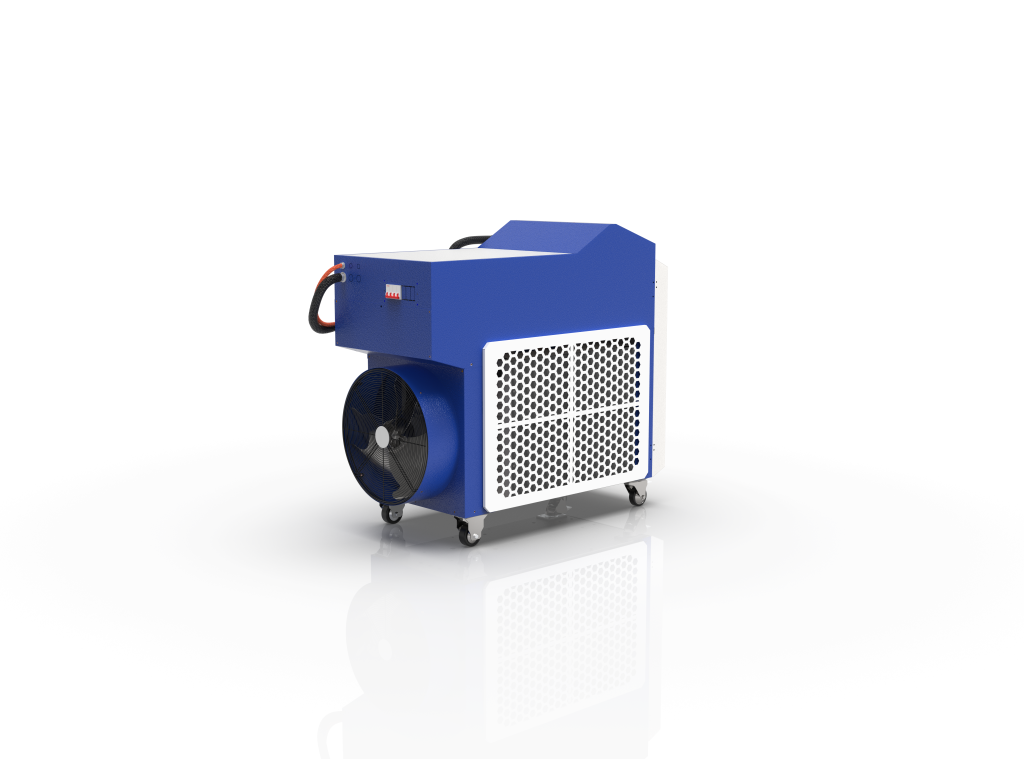
X. Safer in Confined Spaces
Welding in confined spaces can be dangerous. The risk of fire, fume exposure, and accidents increases. Laser welding machines are ideal for these environments. Their precision allows for safer welding in tight areas. Auto laser welding machines can be programmed to work in confined spaces, eliminating the need for human entry.
XI. Reducing Fatigue and Injuries
Manual welding can lead to worker fatigue, increasing the risk of accidents. Continuous exposure to hazardous conditions can cause injuries. Laser welding machines reduce physical strain on workers. Automation allows operators to focus on overseeing the process, not performing it. This reduces fatigue-related accidents.
XII. Training and Skill Development
Using laser welding machines requires proper training. However, once trained, workers can operate these machines with less risk. The need for advanced skills reduces the chances of accidents. Workers develop specialized knowledge, enhancing overall safety in the workplace.
XIII. Future Safety Advancements
As technology advances, laser welding machines will continue to improve. Future auto laser welding machines may include AI-based safety systems. These systems will predict and prevent accidents before they occur. Ongoing improvements will make welding even safer in hazardous environments.
XIV. Conclusion
In conclusion, laser welding machines and auto laser welding machines are revolutionizing safety in hazardous environments. Their precision, automation, and real-time monitoring reduce risks significantly. By minimizing human exposure to dangers, these machines ensure a safer, more efficient workplace. As technology continues to evolve, laser welding machines will play an even larger role in promoting safety.